Blog
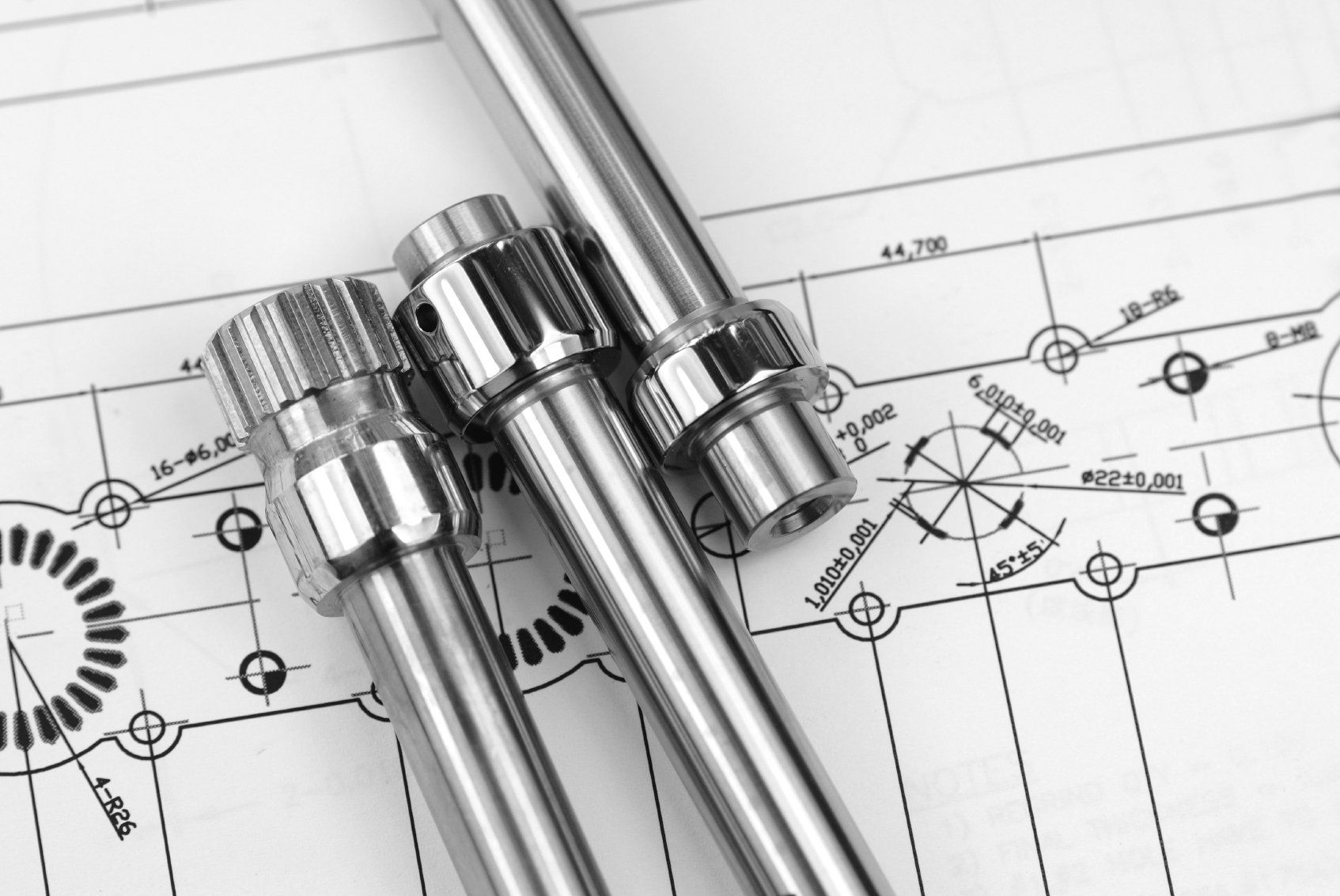
In der Welt des Maschinen- und Anlagenbaus ist Produktvarianz oft ein zweischneidiges Schwert. Auf der einen Seite bieten vielfältige Varianten eine hohe Flexibilität und Anpassungsfähigkeit an die Anforderungen des Marktes. Auf der anderen Seite führt eine hohe Varianz zu einer enormen Komplexität in der Produktion, Logistik und im gesamten Wertschöpfungsprozess. Ein anschauliches Beispiel dafür ist die Herstellung von Fräsmaschinen, bei denen selbst kleine Änderungen in den Bauteilen oder Spezifikationen zu erheblichen Herausforderungen führen können. Das Problem der hohen Produktvarianz In vielen Unternehmen im Maschinenbau ist es üblich, eine breite Produktpalette anzubieten, die auf die spezifischen Bedürfnisse der Kunden zugeschnitten ist. Doch diese Vielfalt kann die Produktion verlangsamen und die Effizienz mindern. Häufig müssen für jede Variante unterschiedliche Fertigungsprozesse, Materialien, Werkzeuge und Maschinen eingesetzt werden. Dies führt nicht nur zu längeren Produktionszeiten, sondern auch zu einer höheren Fehleranfälligkeit und einem gestiegenen Schulungsaufwand für Mitarbeiter. Ein weiteres Problem entsteht in der Logistik und Lagerhaltung: Verschiedene Varianten erfordern unterschiedliche Bestände an Bauteilen und Komponenten, was zu höheren Lagerkosten und einer schwierigeren Bestandsverwaltung führt. Die fünf wichtigsten Vorteile einer Standardisierung Die Standardisierung von Produktgruppen bietet eine Lösung für diese Herausforderungen. Am Beispiel einer Fräsmaschine lässt sich gut aufzeigen, wie sich eine konsequente Produktstandardisierung positiv auf die gesamte Wertschöpfungskette auswirken kann. 1. **Kostensenkung** Eine Standardisierung ermöglicht eine Optimierung der Produktion. Durch die Reduzierung der Varianten können Prozesse effizienter gestaltet und Teile in größeren Stückzahlen gefertigt werden. Dies führt zu Skaleneffekten und reduziert die Produktionskosten pro Einheit. 2. **Vereinfachte Logistik und Lagerhaltung** Mit weniger Varianten entfällt die Notwendigkeit, unterschiedliche Bauteile in großen Mengen vorzuhalten. Eine Standardisierung ermöglicht es, die Lagerhaltung zu straffen und die Logistikprozesse zu vereinfachen, da weniger unterschiedliche Komponenten transportiert und gelagert werden müssen. 3. **Schnellere Montage** Die Montage einer standardisierten Fräsmaschine wird deutlich einfacher und schneller, da immer wieder die gleichen Bauteile zum Einsatz kommen. Weniger Varianten bedeuten weniger Komplexität beim Zusammenbau, was zu einer Reduzierung der Montagezeiten führt. 4. **Verbesserte Qualität und Fehlerreduktion** Mit weniger Varianten wird die Fertigung konsistenter und fehlerresistenter. Durch die Wiederverwendung von Komponenten und die Vereinheitlichung von Produktionsprozessen können Qualitätsschwankungen vermieden werden. Dies steigert die Zuverlässigkeit der Maschinen und führt zu einer höheren Kundenzufriedenheit. 5. **Bessere Planbarkeit und höhere Flexibilität** Eine standardisierte Produktion ist leichter planbar. Unternehmen können Engpässe besser vorhersehen und ihre Ressourcen effizienter einsetzen. Gleichzeitig bleibt die Flexibilität erhalten, da Kundenwünsche in ein standardisiertes Produktportfolio integriert werden können, ohne die gesamte Produktionsstruktur neu ausrichten zu müssen. Die Ergebnisse der Standardisierung am Beispiel einer Fräsmaschine Stellen wir uns vor, ein Unternehmen im Maschinenbau entscheidet sich, die verschiedenen Varianten seiner Fräsmaschinen zu standardisieren. Zunächst werden die gemeinsamen Kernkomponenten identifiziert, die für alle Modelle benötigt werden. Dazu gehören beispielsweise das Maschinenbett, der Motor, das Steuerungssystem und bestimmte Werkzeugaufnahmen. Nach der Standardisierung stellen sich mehrere positive Ergebnisse ein: - **Reduzierte Produktionskosten**: Durch die einheitliche Verwendung von Komponenten und eine vereinfachte Fertigungslinie sinken die Produktionskosten erheblich. Die Firma spart nicht nur Materialkosten, sondern auch Personalkosten durch optimierte Arbeitsabläufe. - **Effizientere Logistik**: Anstatt unterschiedliche Bauteile für jede Maschine zu lagern, wird ein zentraler Bestand an Komponenten aufgebaut. Dies senkt Lagerhaltungskosten und verringert die Komplexität der Lieferkette. - **Schnellerer Montageprozess**: Der Montageaufwand sinkt durch die Verwendung standardisierter Komponenten. Techniker müssen weniger auf Variationen achten, und der Zusammenbau erfolgt effizienter. - **Weniger Fehler**: Durch die Standardisierung sind die Fertigungsprozesse stabiler und weniger anfällig für Fehler. Die Qualität der Maschinen ist gleichmäßiger, und es treten weniger Reklamationen auf. Fazit Die Standardisierung von Produktgruppen, wie es bei der Fräsmaschine beispielhaft gezeigt wird, hat viele Vorteile. Sie reduziert nicht nur die Komplexität in der Produktion, sondern auch die Logistik- und Lagerkosten. Die Vorteile der Standardisierung kommen sowohl den Herstellern als auch den Kunden zugute, da sie zu einer höheren Qualität, schnelleren Lieferzeiten und letztlich auch zu einer besseren Wettbewerbsfähigkeit führen. Wenn auch Sie die Komplexität in Ihrer Produktion reduzieren möchten, könnte eine gezielte Standardisierung der Produkte ein entscheidender Schritt sein. Nutzen Sie die Chancen der Effizienzsteigerung und Kostensenkung – Ihre Firma wird es Ihnen danken!
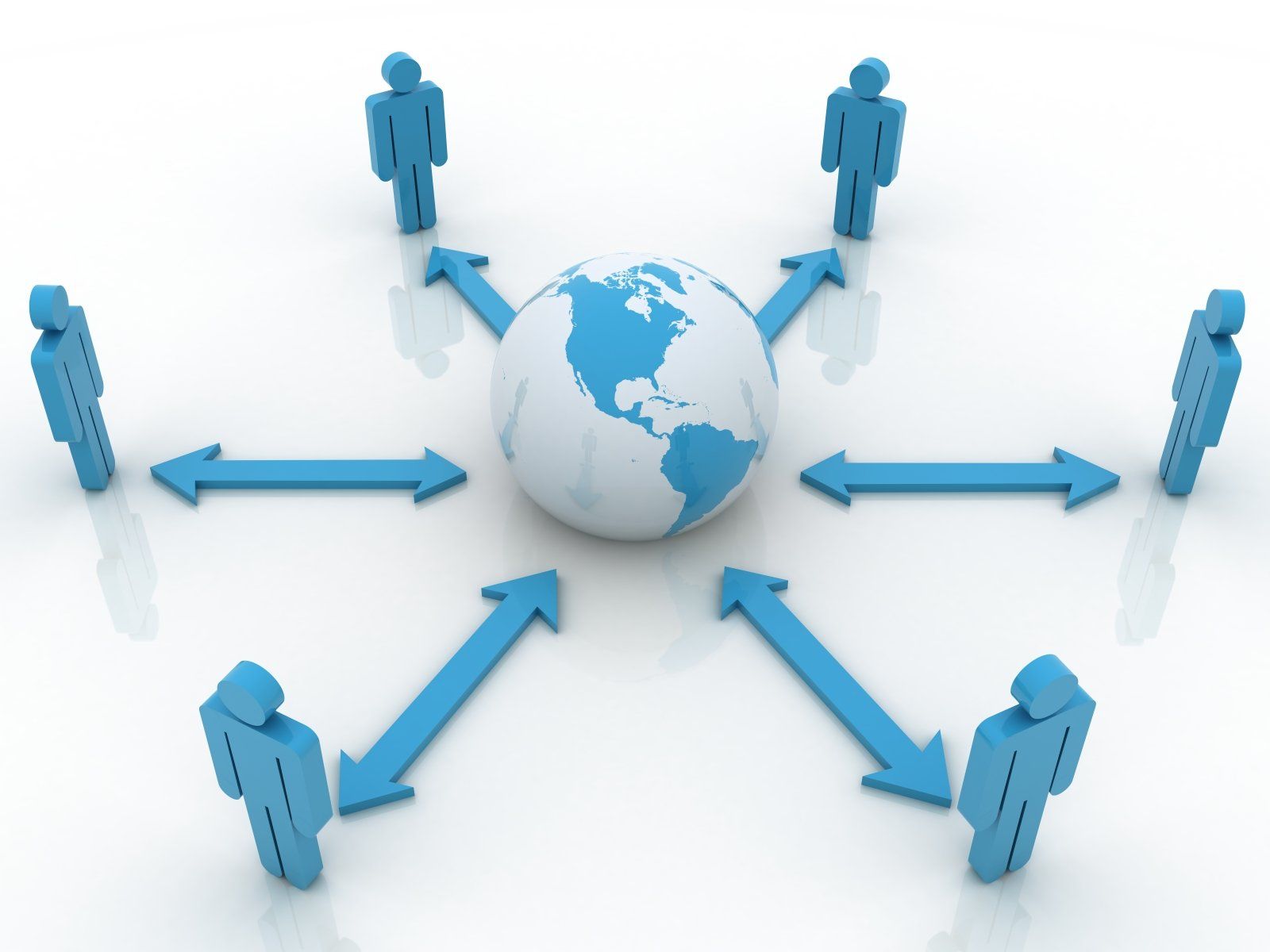
Chaotisches Situationen in Unternehmen und Systemen sind alltäglich. Um mit diesen Chaos umgehen zu können, muss die Komplexität reduziert werden. Oftmals wird versucht mit ungeeigneten Mittel die Dinge zu vereinfachen oder es wird nicht erkannt, dass es sich um eine chaotische Situation handelt. Dadurch wird das Problem nicht gelöst und im schlimmsten Fall kommt das Unternehmen sehr schnell in eine Schräglage. Darum hier in dem Blog eine kurze Darstellung, was zu beachten ist.
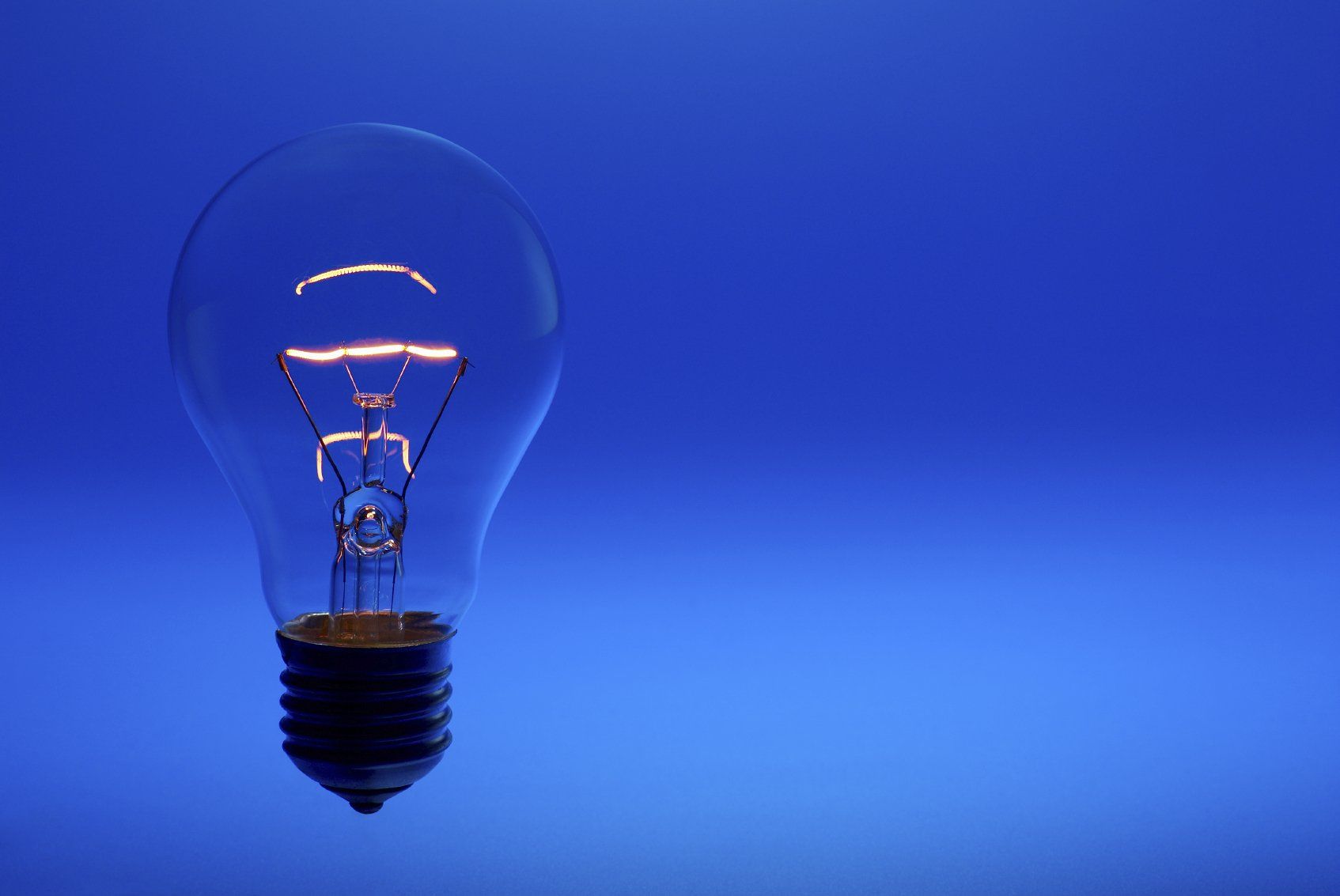
Der Übergang von einem komplexen Zustand in einen komplizierten Zustand ist für ein Unternehmen ein entscheidender Schritt, um ein stabiles Umfeld zu schaffen. Wichtig ist dabei zu beachten, dass Teile des Unternehmens, wie Marketing & Vertrieb in einem komplexen Umfeld operieren und auch dort zu belassen sind. Während es für den operativen Bereich, wie Produktion oder Einkauf entscheidend ist in einem geordneten Umfeld zu arbeiten. Dafür muss eine klare Schnittstelle geschaffen werden, der das Komplexe in Komplizierte Strukturen umsetzt. Ansonsten entsteht ein hoher Koordinations- und Organisationsaufwand und damit hohe Reibungsverluste in der Organisation
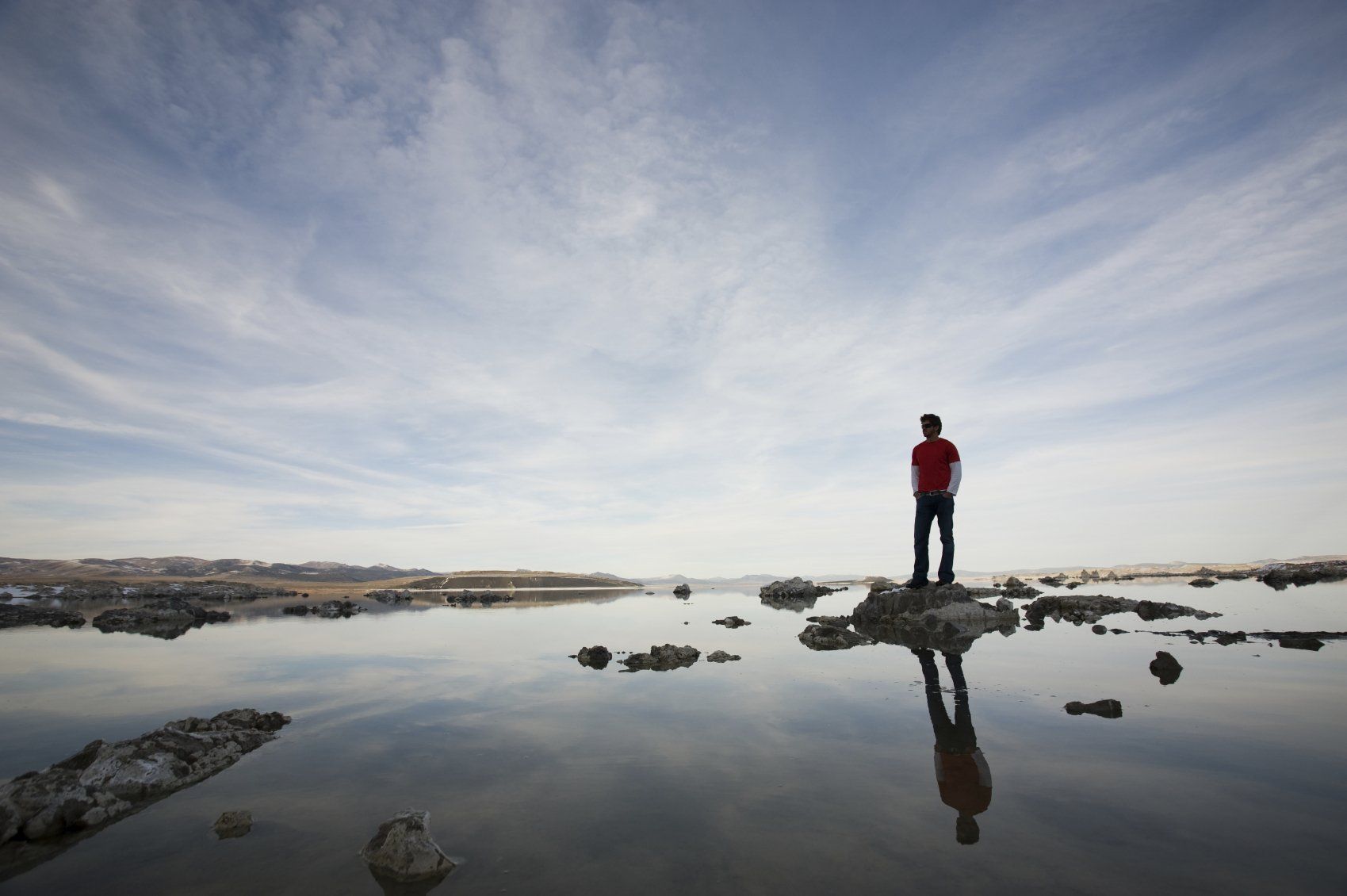
Wir leben in einer Welt in dem die einzelnen Elemente miteinander verbunden und verwoben sind. Ein mangelndes Verständnis der Zusammenhänge und Abhängigkeiten führt zu Orientierungslosigkeit und Angst. Der Mensch sucht nach Orientierung, Ordnung und Halt, um sich sicher zu fühlen und Vertrauen in die Gesellschaft und in die Zukunft zu finden. Wir geben hier eine kleine Orientierung, wie solche Situationen zu bewältigen sind. Dies dient auch der mentalen Vorbereitung auf andere chaotische Situationen als kann somit als Richtschnur dienen. Wer das Worst-Case-Scenario im Kopf hat, ist vorbereitet auf kritische, chaotische Situationen und wird somit eher mit solchen Situationen zurecht kommen. ----- Wenn wir „gesellschaftliches Chaos“ meinen, denken wir an Situationen wie: Zusammenbruch staatlicher Ordnung Revolutionen oder Putsche Kriege oder Bürgerkriege Extrem schnelle soziale, wirtschaftliche oder technologische Umbrüche Informationschaos & Vertrauensverlust in Institutionen Also Umfelder, in denen Regeln, Normen und Orientierung wegbrechen – und die Menschen individuell und kollektiv ins Schwimmen kommen.